Injection moulding
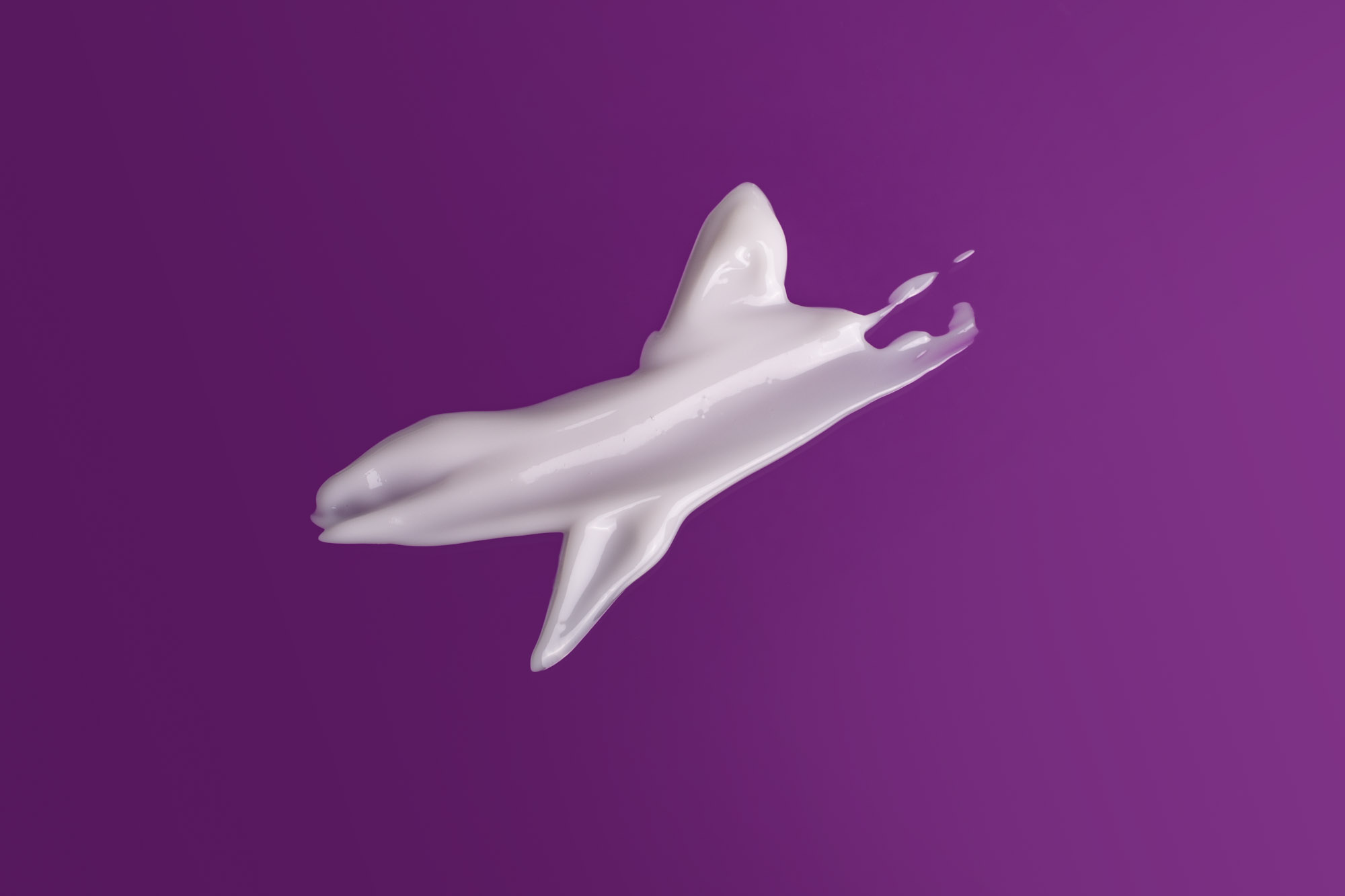
What is injection moulding?
Injection moulding is the process of manufacturing highly accurate plastic components such as closures, overcaps, and reducing plugs. Plastic resin is fed into a heated barrel and screw which is then injected at high pressure into a water-cooled mould which may consist of various moving parts.
Due to the high injection pressures, this cavity will be held together by the use of a clamping unit. While the plastic is held inside the mould, the plastic will freeze off to the desired shape. After the plastic has cooled sufficiently, the mould and clamping unit will open and allow the finished component to be ejected so that the process can be repeated.
Which materials can be injection moulded?
Polypropylene (PP) is the most common resins used in injection moulding and can be divided into three sub categories:
- Homo polymer: For general use of moulding closures
- Co Polymer (Random): Gives excellent clarity when used for overcaps and when closures are used with active hinges as with 'flip top' closures
- Co Polymer (Block): These components will generally have poorer clarity and are therefore generally coloured components but offer greater impact resistance
Generally PP is advantageous when being used in conjuction with a dissimilar bottle materials such as HDPE, PVC or PETG as it will improve any binding issues between the two components.