Injection stretch blow moulding (ISB)
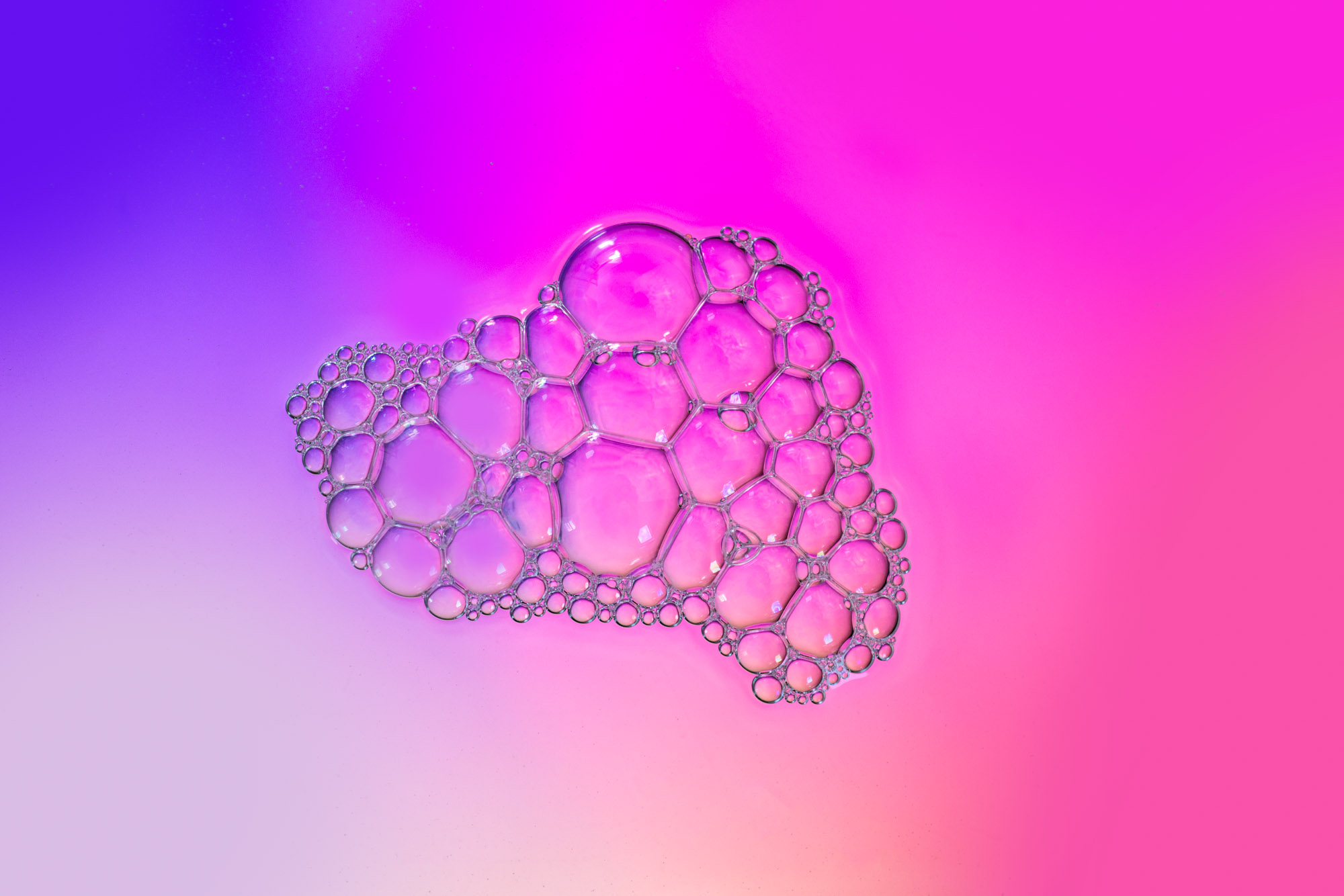
Injection Stretch Blow Moulding (ISB) is a process that manufacturers high quality containers in PET to produce a clarity similar to glass.
ISB can also produce materials that are less clear such as polypropylene (PP).
Production process
Production begins with the injection process, where molten polymer flows into an unjection cavity to produce a preform, a hollow test tube shaped plastic object that has a neck and a thread on the open end.
When the preform is conditioned to the correct temperature, it is ready for stretching and blowing to the desired shape using a mould. Once in the mould, a rod is introduced to stretch the preform using two levels of air pressure, the preform is then blown circumferentially. After a set cooling time, the moulds open and the preformed bottle is removed. The process is carried out concurrently using a revolving carousel of moulds.
ISB is an environmental alternative to glass
Because plastics are soft and boast lower melting points, PET bottles require less energy to manufacture than glass. Easier to recycle, PET can also be made in PCR in levels up to 100%.
It is also possible to make PET products using a range of biopolymers, including sugarcane based PET. With no sign of difference in both appearance or performance, out PET biopolymer can be recycled in the same stream as conventional PET and PCR PET, for a truly sustainable solution.
What are the advantages of this process?
Offering dimensionally accurate bottle shapes, when molded, PET (Polyethylene Terephthalate) provides an excellent alternative to glass for a number of reasons
These include:
- Clarity similar to glass
- Lighter in weight
- More cost effective to transport products
- Higher breakage resistance to avoid risk and injury
- More durable than glass
- Excellent barrier characteristics against carbon dioxide and oxigen
- Requires less energy to produce
- Can be easily recycled
- PET can be decorated with silk screen printing and hot foil blocking